En la práctica realizada en esta asignatura con el profesor Julio Juan García Sabater pudimos, entre otras cosas, ver de primera mano el funcionamiento del kanban y del sistema pull. Algunas de las cuestiones que abordamos aquel día era que para cada loop deberíamos poner un kanban con un Q diferente, y que el kanban necesita holgura para que el sistema funcione de manera correcta, sobre todo si introducimos en el sistema piezas especiales (críticas o urgentes).
Ello me hizo recordar un capítulo que aparecía en el famoso (y recomendado) libro “Las claves del éxito de Toyota” de Jeffrey K. Liker, donde se explica de manera muy sencilla el concepto de kanban y pull aplicado a la vida cotidiana, una manera muy afortunada de desmitificar estos conceptos tan abstractos que vemos en el máster.
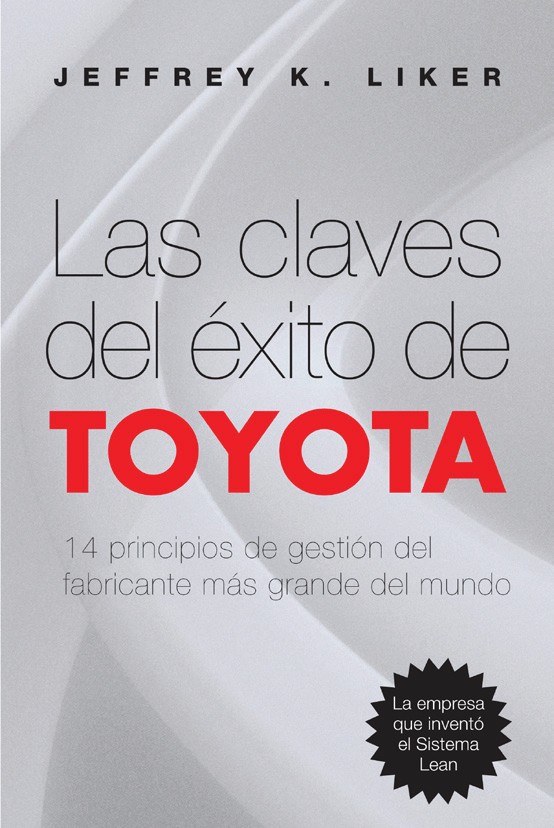
Dentro del principio 3 de Toyota, «utilizar sistemas pull para evitar producir en exceso«, se nos plantea el siguiente problema: cuando se decide comprar gasolina para el coche, ¿se rellena el depósito de acuerdo a una planificación o se podría considerar llenar el depósito simplemente una vez por semana, por ejemplo, los lunes por la mañana? Es muy improbable que alguien use este método, ya que si se hiciera se observaría que a veces no se necesita realmente la gasolina los lunes por la mañana, mientras que otras veces nos quedaríamos sin ella antes del lunes. Lo más común es que cuando sé que el indicador de la gasolina se está acercando a 0, pare en una estación de servicio a repostar. Pues el mismo comportamiento del sistema pull funciona para la mayoría de las cosas rutinarias. El desencadenante es, simplemente, que vemos que el nivel del stock de un artículo nuestro está bajo y, en un momento dado decimos “será mejor que vaya y pida un poco más de esto”.
Con esto tampoco significa que todo puede ser rellenado basándose en un sistema pull. Algunas cosas deben ser planificadas. Siempre que se esté comprando un artículo especial o de un solo uso hay que pensar que es lo que se desea, considerar los costes y los beneficios, y planear cuándo comprarlo. Es decir, se crea una planificación para comprar algo, debido a que no existe una necesidad inmediata de ello.
Los servicios son otro tipo de compra que no es inmediata, pero debe ser planificada. Por ejemplo, si queremos limpiar una fosa séptica no existe ninguna forma de conocer si está llena y si requiere de un vaciado. De este modo, por lo general, se recurre a la planificación (que puede ser incorrecta) para la limpieza de la misma. No obstante, desde hace unos años existe un dispositivo en el mercado que puede ser instalado para detectar el nivel de la fosa séptica, de manera que cuando se alcanza el punto de pedido, se indica a través de una señal de radio el momento en que se requiere de su limpieza. Si se instala este dispositivo se puede eliminar la necesidad de un sistema de planificación y se puede sustituir por un sistema de rellenado por sistema pull con una señal para rellenar (vaciar, en este caso) basado en el uso actual.
Con este sencillo ejemplo en el capítulo se explica como Toyota trabaja constantemente para alcanzar el ideal de rellenado just-in-time. Usando kanban se está:
- monitorizando y coordinando detalladamente el uso y rellenado de miles de piezas y herramientas
- organizando planificaciones específicas para el rellenado
- desarrollando reglas para determinar el momento de enviar la señal pull de llenado
- calculando la máxima cantidad de inventario permitido
- …
En la mayoría de casos el sistema kanban/pull trabaja mejor que un sistema de planificación. Aunque siga dependiendo de pequeños buffers de inventario o “almacenes de piezas”, el inventario es siempre un compromiso. De esta manera la meta es eliminar el “almacenado de piezas” y conseguir un flujo de pieza a pieza (one-piece-flow) allí donde sea posible. Para que sea más ilustrativo, en este sencillo vídeo podemos ver cómo se emplea un kanban de 4 piezas en un entorno industrial que funciona con un sistema pull.
Espero que estos ejemplos y conclusiones te hayan sido interesantes.
¡Gracias por leer el post!
Javier Navarro Martínez